AAC Block | Properties | Manufacturing Process | Merits and Demerits | Precautionary Measures| Cracks | Final Words |
Construction and Infrastructure projects today can recognize even the most intricate and complex concepts. Nevertheless, the capacity of the project director and manager and all others engaged in discovering the sufficient resources and equipment that go along with its creation directly determines the sustainability of these initiatives.
The newest development in the construction sector, AAC blocks, maybe everyone looking for the answer. AAC blocks are a compact alternative to red clay bricks for wall use. They also have excellent thermal insulation qualities, allowing the building’s interiors to be much more relaxed than the surrounding area.
Check out the details on what is meant by 1 bigha land and what is bhunaksha.

What is an AAC Block?
AAC, popularly known as Autoclaved Aerated Concrete, is a construction material that is certified, eco-friendly, and more durable and renewable. AAC blocks are a kind of foam concrete, sustainable precast, created with a collection of lime, water, quartz sand, aluminium powder, portland cement, and calcined gypsum.
All these materials are moulded and mixed correctly, and it is heated, thus forming the final concrete block and getting its primary form. These blocks are in high demand, and people prefer them because of their properties. This construction material is used for both exterior and interior building construction.
AAC Block Properties
Autoclaved Aerated Concrete blocks can be utilised for private business and the modern development of building structures. Its basic properties make it a structured and sustainable segment. Following are the properties of AAC block –
- High solidarity due to the use of various concrete and strong materials.
- Steel support and huge weight proportion because of the solid items.
- The thermal resistance of the high range and provides around the thickness of significant rate.
- High compressive strength due to the quality of the materials.
- The water absorption level is average.
- Its thermal efficiency makes it 3x times more than the other bricks like clay, red bricks, etc.
Manufacturing Process of AAC Block
Materials used in manufacturing AAC blocks are as follows –
Fly ash | It is an industrial product that is used in the reduction of building construction. The density varies in various ranges. Fly ash provides fire resistance, sound absorption, and insulation. |
Aluminum Powder | Aluminium is an augmentation force. When all the raw materials are mixed and reacted with this powder, air bubbles are formed between water, calcium hydroxide, and aluminium. Finally, the hydrogen gas is evaporated. |
Cement | There are various blocks of cement in the market that are available. You must opt for the suitable one for manufacturing AAC Blocks. The preferred adhesive is OPC grade 53, which is helpful in hardening, binding, and setting the materials. |
Limestone | You can obtain this material by crushing limestone to fine powder or by purchasing the powder from the market. |
Step-1: Preparation of Raw Materials
The manufacturing process of autoclaved aerated concrete blocks is unique and precast at the same time. It is manufactured by aggregating materials like gypsum, water, fly ash, cement, aluminium powder, lime, etc., where all of these are poured and combined into a mould form.
Step-2: Mixing, Casting, and Curing the Materials
Once all these materials are combined with the concrete particles, aluminium power starts reacting with fly ash and lime, producing hydrogen bubbles with millions of microscopic small particle-like structures.
Step-3: Evaporation and Cutting of the blocks
The formation of hydrogen bubbles helps the concrete to enlarge roughly compared to the original volumes, following the hydrogen to evaporate, leaving the concrete structure in the aerated form. After this, the concrete is cut and made into blocks that are cured and steamed into an autoclave.
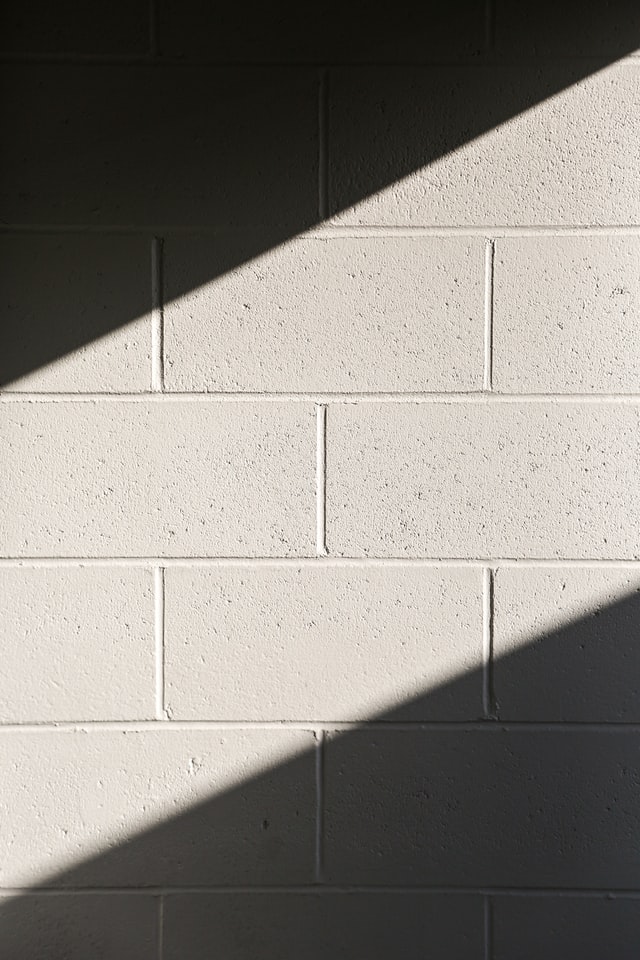
Merits and Demerits of AAC Block
These construction blocks are famous for their qualities, and they have many advantages and some disadvantages as well. So let us have a look at the merits and demerits of AAC Block.
Merits
Fire Resistant
AAC blocks are fire-resistant and non-combustible with a temperature of up to 1600 degrees celsius. With this, they can withstand direct exposure for six hours.
Sustainable, Eco-friendly, and Affordable –
The use of fly ash and other non-toxic material usages with no gas emission and less energy absorption makes these blocks sustainable and eco-friendly. By using non-toxic, natural, and inorganic raw materials, the manufacturing process of AAC Blocks generate minimum or less wastage. They can be recycled and used again.
Faster Construction –
As these blocks are available in various sizes, it reduces construction time by a significant percentage. As a result, its lightweight property makes it faster and easier to place, transport, and construct a building structure.
Work Easily with Flexible Designs –
Blocks of AAC can be efficiently designed, nailed, grooved, drilled, cut, and milled to fit individuals’ specific needs and requirements. These blocks also have consistent measurements and dimensions, ensuring easy laying.
Seismic or Earthquake Resistant –
Non-combustible nature of AAC blocks provides many advantages and makes them seismic resistant. For example, it reduces the earthquake impact on a building or construction site because of its lightweight. During the manufacturing process, these blocks gain high-level strengths providing durability to the structures.
Acoustic Performance –
Autoclaved aerated concrete block observes superior sound absorption blocking all other significant disturbances and sounds. It is also porous. This makes it ideal and easy to construct offices, schools, hotels, multi-family housing, hospitals, and other structures requiring audible insulation.
Moisture Proof –
With the help of macro-pores, AAC block shields use low water absorption providing the structure with moisture protection in various ways. These blocks will be more useful in the rainy season as the leagues require high water absorption capacity to stay durable. However, it is possible with AAC provided if it is manufactured correctly.
Efficient Energy and Thermal Insulation –
Blocks of thermal mass and pores of tiny air give rise to spectacular thermal insulation. This will reduce air-conditioning costs and heat a building for specific purposes.
Lightweight –
When you compare AAC blocks with bricks like red or clay, these are 3-4 times less weight. Also, they are 30% lighter than concrete, which helps build load reduction. This makes it easier and allows the smooth construction of taller and heavier buildings.
Cost Saving –
Because of the lightweight and flexibility in transportation, these blocks save a lot on shipping costs and overall logistics compared to traditional clay bricks or red bricks’ transportation. With the high insulation property, these blocks save a lot on energy costs resulting in the minimisation of steel and cement materials.
Pest Resistant –
AAC helps protect the building structures from pests like rodents, termites, etc., as the blocks are prepared from inorganic materials. This helps in avoiding losses and damages.
Demerits
- Brittle in Nature – AAC Blocks are brittle and fragile. These need to be properly and carefully handled compared to others, like clay bricks, to avoid cracks and breakage. This nature of the blocks will require thinner and longer screws while fitting wall hangings or cabinets.
- High Cost Per Unit – The CPU or Cost per unit of autoclaved aerated concrete blocks is high compared to the cost of masonry, which is low due to less requirement of mortar for the installation process.
- Material with non-load bearing – As AAC is a non-load bearing material, it can only be used for wall partitioning. Therefore, these blocks should be carefully handled and transported to a safe place with an unlabeled surface.
- Cracks after Installation – These blocks are known for damage after installation in rainy weather. You can avoid these cracks by reducing or cut-shorting the mortar strength. Also, ensure that the blocks are dry during the whole installation process.
Precautionary Measures
Following are the precautionary measures for autoclaved aerated concrete blocks –
- Do not use these construction material blocks for laying the foundation, water tank, drainage pits, etc., where there is excessive dampness.
- Use these blocks with stiffener columns for every length of 3-meters.
- Do not use rich and thick mortar to avoid shrinks and cracks in the wall.
- Do not use these blocks for storage on unspecified surface areas.
- Use RCC beams by using steel reinforcement for uniformly distributing wall loads to avoid all types of cracks.
- Use high-quality cement materials like portland pozzolana to get better results.
- Do not use AAC blocks for structures that you will use for load-bearing purposes where you do not make use of columns or beams.
Cracks in AAC Blocks and how to prevent them
Although the material is of high quality, sometimes, there may be some cracks because of the following –
- Dry Shrinkage Issue – AAC blocks need around 15 days of drying and 28 of curing to maintain their thickness and for contracting and expanding. If the manufacturing process is not followed correctly, the material may not be delivered on time for construction, and there are many chances of these blocks getting cracked.
- Brittle Nature – These AAC blocks are delicate and fragile sometimes because they may break easily. In such cases, they may also fail if they are dropped off from low heights.
- Cement Mortar Usage – For installing these concrete blocks, you can use cement mortar as a sticky material to avoid cracking.
AAC is a bearing non-load material. So, you should use reinforced concrete cement or similar material as a stiffener with thickness to support AAC after every step of its manufacturing process.
Related: All About einvoice1.gst.gov.in Website
Final Words
The construction projects sector’s most innovative, sustainable, and efficient building material is AAC, known as autoclaved aerated concrete. Fly ash, reprocessed industrial effluents, is used productively to create AAC blocks, which qualify as a sustainable construction material.
AAC blocks’ intrinsic qualities lead to quick and effective construction methods. As a result, AAC is now a helpful building material utilised in various commercial, industrial, and residential structures. In addition, AAC can be referred to as a cleaner and greener material for construction because it uses easily accessible raw materials more efficiently in manufacturing and production.
AAC material also has good durability, is environmentally friendly, is affordable, and can be regenerated. Due to the rising desire for residential and industrial space, AAC blocks are becoming increasingly preferred in many Asian nations, particularly India. AAC is like a cutting-edge construction material.
It has unique qualities that enable it to be superior to conventional bricks and provide a structural system with numerous protections. Countries including Germany, the United States, India, and Russia manufacture these specialised blocks on a large scale for building materials. But in India, the marketplace for these structural materials is still very much in its infancy.
Related: Parivar Pechchan Patra Haryana